Tornitura conica
Per la tornitura conica (produzione
di un pezzo a forma conica), tolta la spina G, si sblocca la vite
sottostante
alla trasmissione e si gira la testa dell' angolo necessario, fissandola
nella nuova posizione.
Il lavoro procede poi come nella normale torni tura cilindrica.
Anche la tornitura conica può essere eseguita all'auto centrante, oppure fra
le punte.
Limitiamoci ad esemplificare la lavorazione all'autocentrante, perché, con
quel che ormai sappiamo
e quel che vedremo qui appresso, è facile estendere l'applicazione all'altro
caso.
Come esercizio, proponiamoci di realizzare il pezzo illustrato nella fig.
15.
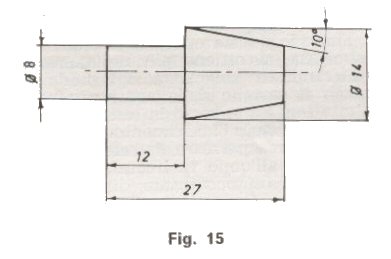
Esso è costituito da un codolo cilindrico con (2) 8 e lunghezza 12 e da una
parte tronco-conica, della quale il disegno indica il diametro massimo (14
mm)
e l'angolo di inclinazione della superficie laterale (10°).
Partendo da una barretta di Ø 15 mm circa, eseguite le operazioni di
intestatura fino a lunghezza di 27 mm, ricaviamo dapprima con lo sfacciato
re sinistro il codolo cilindrico, che prenderemo poi, capovolgendo
il pezzo, nell' auto centrante.
Inserita ora una delle due punte nel cannotto T
della contropunta, spingiamola, facendo scorrere
a mano il castello della contropunta sulle guide K, contro il pezzo, in modo
da produrre un piccolo segno nel centro A del medesimo (v. fig. 16).
Ora si tratta di eseguire un calco letto che ci consenta di stabilire con
precisione di quanto occorra ruotare la testa motrice.
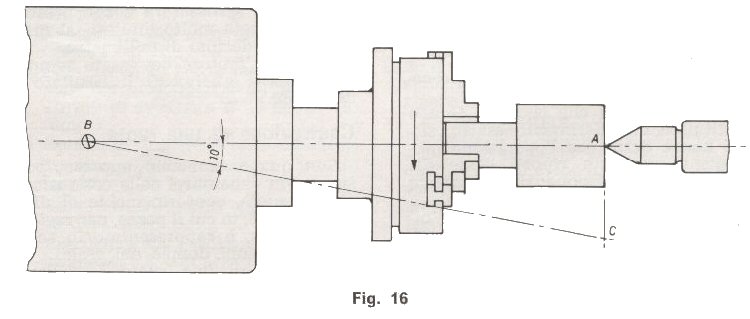
Per angoli piuttosto piccoli, si può procedere prendendo come base lo
spostamento da far subire -rispetto al riferimento costituito dalla punta,
che rimane ferma al suo posto -al segno praticato con la punta stessa nel
centro A del pezzo, che viene ruotato assieme alla testa.
Tornando alla fig. 16, individuiamo il triangolo rettangolo ABC, il cui
vertice B coincide con l'asse di rotazione
della testa motrice (individuabile in una piccola vite situata nella parte
superiore della testa stessa), e la cui ipotenusa BC forma un angolo di 10°
rispetto al cateto AB, che in questa posizione coincide con l'asse della
macchina.
Se ruotando la testa, portiamo in C il punto A del pezzo, l'asse di quest'ultimo
viene a formare un angolo di 10°
con l'asse della macchina e con le guide del carrello: in posizione tale,
cioè, che l'utensile, spostandosi obliquamente rispetto al pezzo, lo lavora
conico (fig. 17).
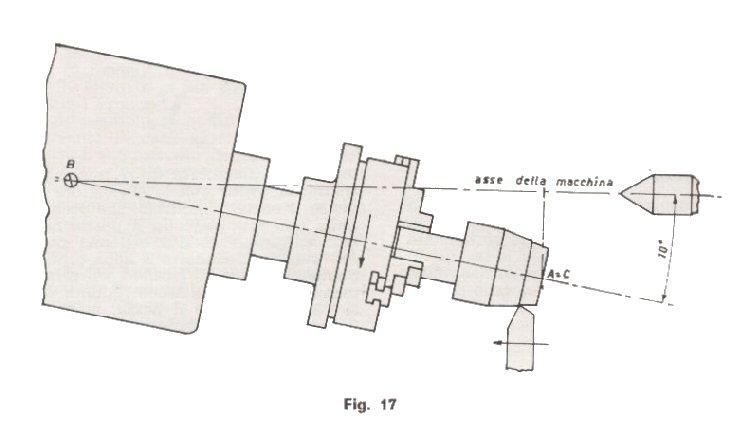
Si tratta ora di calcolare la lunghezza del segmento AC, che misura lo
spostamento da operare e che
indicheremo con s.
Sulle tavole trigonometriche leggiamo il valore della tangente di 10°:
tg 10" = 0.176
Se indichiamo genericamente con a il valore dell'angolo fra cateto AB e
ipotenusa BC (nel nostro caso a = 10°)
e con a la lunghezza del cateto AB (che bisogna misurare sulla macchina e
che supponiamo nel nostro caso
di 90 mm),il valore di s si calcola con la seguente formula:
s = a * tg a (2)
e, nel nostro caso:
s = 90 * 0,176 = 15,8 mm
Sbloccata dunque la testa come detto all'inizio, ruotiamola fino ad ottenere
lo spostamento di 15,8 mm
del punto A del pezzo rispetto al riferimento costituito dalla punta. Se non
ci interessa l'esattezza, potremo arrotondare a 16 mm. Bloccata qui la
testa, procediamo alla tornitura della parte conica a norma di disegno,
cioè fino ad ottenere alla sua base il diametro di 14 mm.
Per allineare nuovamente la testa una volta ultimata la tornitura conica,
ruotiamola indietro, a vite conica allentata, fino a reinserire al suo posto
la spinta G, e blocchiamo poi la vite conica.
Occorre notare che la spina G non costituisce un riferimento esatto, sicché
non è detto che l'operazione ultimamente descritta riporti l'asse del
mandrino in posizione rigorosamente parallela alle guide K del carrello.
Un allineamento rigoroso si può ottenere solo montando un pezzo lungo fra le
punte (com'è stato descritto
al capitolo precedente), eseguendo una tornitura e controllando col calibro
i diametri alle due estremità:
se essi differiscono, bisogna trovare per tentativi la posizione della testa
per la quale la tornitura risulta perfettamente cilindrica.
Essendo questa operazione piuttosto laboriosa, si ottiene più rapidamente un
risultato sufficiente spingendo a mano il castello della contropunta, a
punta innestata, verso la testa motrice fino ad ottenere l'inserimento della
puntamedesima nel foro dell'albero della testa, che all'uopo va liberata da
ogni accessorio (autocentrante,
disco menabrida, ecc.). Operazione più sbrigativa e risultato sufficiente,
abbiamo detto: infatti, non è rigorosa come quella descritta al capoverso
precedente.
Finitura
In precedenza ci siamo dimenticati di osservare -e ciò vale per ogni tipo di
tornitura -che, se si vuole una superficie ben finita, le ultime passate
vanno eseguite con l'utensile finitore, a velocità circa doppia di quella
impiegata per la sgrossatura e con profondità di passata molto limitata, al
massimo di un decimo di millimetro.
L'utensile finitore dev'essere sempre ben affilato, altrimenti il risultato
è deludente.
Costruzione di una ruota
Con quanto abbiamo appreso, possiamo ora cimentarci nella costruzione di una
ruota, conformemente
al disegno di fig. 18, in cui il pezzo, per ragioni di chiarezza, è
rappresentato in scala 2:1
(dimensioni doppie del reale).
Si tratta di
una ruota ferroviaria «a vela piena»,
cioè non a razze.
Per rispettare le buone norme costruttive,
la fascia di rotolamento è prevista conica, con inclinazione di 3°.
Partiamo da un tondo di ottone con g 16 e
lunghezza di 18 -7- 20 mm, che bloccheremo nell'autocentrante.
Quando la costruzione di un pezzo richiede
numerose operazioni -come nel nostro caso -è indispensabile, più che
opportuno, studiarne preventivamente la successione, in modo che
un eventuale erroneo procedimento non
pregiudichi il resto del lavoro. Si deve,
cioè, definire quello che, nel gergo tecnico,
si chiama il ciclo di lavorazione. Vediamo quel che conviene nel caso in
esame.
Esigenza essenziale del caso è che la ruota, una volta montata
sull'assale,giri ben centrata, ovverossia esente da quegli sfarfallamenti
che, oltre a provocare irregolarità di movimento, fanno giustamente
inorridire il fermodellista.
A tal fine, il foro Ø 2 mm per la sede dell'assale e la fascia di
rotolamento dovranno essere perfettamente coassiali. Non sarà essenziale,
invece, la coassialità delle altre zone.
Il ciclo di lavorazione potrà dunque essere il seguente:
1) Intestatura dell'estremità del pezzo;
2) Esecuzione del foro di centratura (vedere fig. 12);
3) Foratura a Ø 2 mm con punta da trapano per profondità di circa 5 mm;
4) Tornitura esterna a g 15 per 5 -7- 6 mm;
5) Rotazione di 3° della testa motrice;
6) Tornitura della fascia di rotolamento;
7) Riallineamento della testa per mezzo della spina G;
8) Esecuzione del gradino anteriore di larghezza 0,5, con abbozzo del mozzo
anteriore g 4;
9) Esecuzione del ribasso di 1 mm nella vela e contemporanea finitura del
mozzo;
10) Segnatura cilindrica del pezzo laddove andrà separato dal tondino, cioè
a circa 5 mm dal bordo libero;
11) Separazione col seghetto della parte lavorata;
12) Montaggio del pezzo sull'autocentrante, prendendo fra le griffe la
fascia di rotolamento;
13) Esecuzione del gradino posteriore e formazione del mozzo posteriore;
14) Intestatura del mozzo posteriore.
Si tengano presenti le seguenti avvertenze.
a) Per regolare la profondità di foratura a Ø 2 mm (fase 3), portare la
punta da trapano, preventivamente disposta nel mandrino PT sulla
contropunta, a contatto del foro di centratura del pezzo;
azionato il mandrino a velocità conveniente, far avanzare la punta da
trapano col volantino U
per cinque giri di quest'ultimo: ad ogni giro, infatti, corrisponde
l'avanzamento di 1 mm.
b) Lo spostamento s necessario per ottenere l'inclinazione di 3" della
test&' motrice, calcolato con la formula (2) nel modo illustrato nel
capitolo «tornitura conica», risulta, essendo tg 3° =0,0524 e ponendo a = 90
mm:
s = 90 .0,0524 = 4,7 mm.
Attenzione, durante la tornitura della fascia (fase 6) a non asportare anche
il bordino!
Per la tornitura, si usi lo sgrossatore sinistro, che, opportunamente
disposto, conferisce anche al bordino
una conveniente inclinazione. Con cauta azione di lima, a pezzo rotante, si
arrotondino poi gli spigoli.
c) Per il ribasso nella vela (fase 9), occorre un utensile a punta speciale,
che non rientra nella normale dotazione e che il modellista esperto
puòcostruirsi da sé. Ai principianti consigliamo di tralasciare questa
operazione: la soddisfazione del lavoro non ne soffrirà gran chè.
d) La separazione della parte lavorata (fase Il) si fa più agevolmente a
pezzo rotante, appoggiando la lama del seghetto nel segno anulare prima
eseguito( fase 10). Ma... attenzione a non farsi scappare il seghetto! A
parte possibili lesioni alle mani, c'è di che rovinare completamente il
pezzo!
e) Non stringere troppo le griffe sulla fascia di rotolamento, per non
rischiare di segnarla profondamente, in quanto le griffe toccano la fascia,
per via della conicità, solo nella zona di imposta del bordino. Ciò impone
cautela nella fase successiva, che va eseguita a passate molto leggere.
Un interessante metodo di costruirsi ruote a vela piena in serie è descritto
sul Sito Rotaie.it di Giorgio Donzello.
Merita
una visita al link
http://www.rotaie.it/New%20Pages/Pantografo%20per%20Tornio.html
AL |