Tornitura interna
Giacché siamo... lanciati, passiamo ad un altro tipo di operazione: la
tornitura interna.
Per risparmiare materiale (con quel che costa l'ottone...), seguitiamo a
lavorare sul pezzo appena ottenuto,
nel quale vogliamo praticare un foro assiale del diametro di 9 mm (0 9).
Prendiamo il pezzo nell'autocentrante, lasciando un paio di mm fra
l'estremità interna e la piattaforma.
Sul cannotto T della contropunta avvitiamo il mandrino a tre griffe per
punte da trapano, accessorio noto
a tutti (per brevità, lo chiameremo, nel seguito, mandrino PT), e poniamo in
esso una «punta da centro»
da 1,5 o 2 mm, reperibile in un qualsiasi negozio di ferramenta.
Allentata la vite S, facciamo scorrere il supporto R sulle guide K fino a
toccare il pezzo con la punta da centro; blocchiamo la vite S e, messo in
moto il mandrino a velocità moderata e allentate le viti E, spingiamo
lentamente con la leva F il pezzo rotante contro la punta da centro, fino a
scavarvi un piccolo cratere
(tratteggiato nella fig. 12).
Sostituiamo
ora la punta da centro con una punta da trapano 0 3 e foriamo il pezzo per
tutta la sua lunghezza, operando nello stesso modo che abbiamo descritto per
la centratura. Il foro di centraggio, ricavato precedentemente, ha lo scopo
di creare un'imposta per la punta da trapano, ,che altrimenti scivolerebbe
sulla superficie del pezzo, si distorcerebbe e, comunque, attaccherebbe
probabilmente il materiale in posizione scentrata. Disposta poi nel mandrino
PT una punta 0 6, ripetiamo l'operazione di foratura; ultimata la quale, il
pezzo avrà un foro assiale 0 6. La foratura è stata prevista in due tempi,
essendo poco probabile che un principiante riesca con 1'UNIMA T ad 'eseguire
d'acchito un foro 0 6.
In questa operazione, il tornietto lavora da «trapano sensitivo»: con la
differenza che, nel trapano vero e proprio, il pezzo è fermo e la punta gira
avanzando verso di esso, mentre qui avviene il 'contrario: ma è intuitivo
che ciò non ha nessuna importanza agli effetti del lavoro. Il trapano si
dice «sensitivo», in quanto l'azione manuale sulla leva è affidata alla
sensibilità dell'esecutore, il quale deve imparare a graduare istintivamente
la pressione sulla leva medesima.
Il mandrino PT dell 'UNIMA T non può prendere punte oltre il 0 6: se ciò
fosse possibile, si potrebbe giungere alla quota voluta con successive
operazioni di foratura. Nel nostro caso, invece, dovremo completare il
lavoro mediante tornitura interna, che, in definitiva, è proprio
l'operazione che vogliamo descrivere; ma essendo essa più lenta della
foratura, conviene giovarsi di quest'ultima fin che è possibile.
Monteremo, dunque, sul portautensili l'utensile per foratura interna, ma non
del tipo illustrato in fig. 7, utilizzabile solo per cavità di diametro
assai più grande. A noi serve un utensile di forma particolare, come quello
che appare nella fig. 13, tecnicamente denominato «utensile a stelo con
testa a profilo costante»: utensili di questo tipo si possono trovare negli
empori di ferramenta, che esistono solo nelle grandi città (dai quali,
tuttavia, ci si può rifornire per corrispondenza).
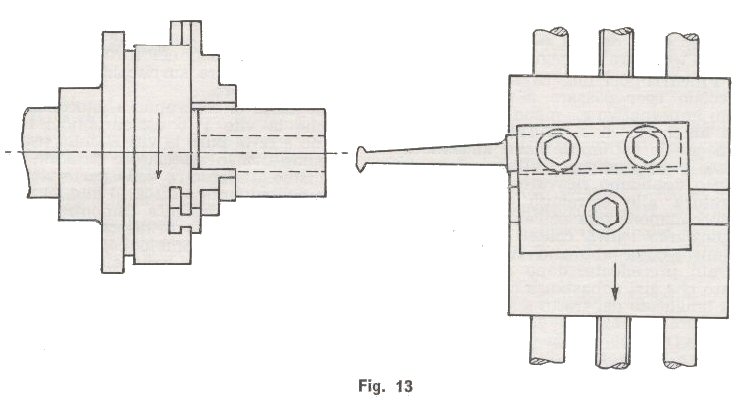
Sistemiamo ,dunque un tal tipo di utensile come mostra la fig. 13 (pianta),
verificandone l'altezza della punta come precedentemente suggerito: si noti
che l'asse dell'utensile è quasi parallelo all'asse del mandrino.
Prima di montare il portautensili, stringiamo la vite della slitta M fino a
rendere leggermente dura la manovra del volantino N. Assicuriamoci che le
viti E siano ben serrate e, con la consueta manovra di J e N, infiliamo la
punta dell'utensile nel foro del pezzo e registriamone la posizione fino a
sfiorare la superficie interna del foro, poi con J
portiamola fuori dal pezzo.
La scelta della velocità di lavoro si fa con la formula (1)
del capitolo III, nella quale al posto di D si
mette il diametro del foro.
Con N diamo uno spostamento ad M verso di noi di 0,1 mm ed eseguiamo la
prima passata completa nel foro,
il cui diametro aumenterà di circa 0,2 mm. Riportato il carrello al punto di
partenza, altro spostamento su N
di 0,1 mm e seconda passata; e così via, fino a raggiungere il diametro
voluto.
Per controllare il procedere del lavoro, possiamo usare, fra una passata e
l'altra, il calibro a corsoio, che è munito di due appendici (non
riprodotte, per semplicità, nella fig. 8) idonee appunto alle misure di
interni, come
mostra la fig. 14.
Due parole
sulla precisione dello strumento.
Il calibro a corsoio, nella sua versione ordinaria, raggiunge
l'approssimazione del decimo di mm: è pertanto sufficientemente preciso se
ci basta che il diametro del foro sia compreso fra un decimo di mm in più e
un decimo di mm in meno del valore richiesto
(9 mm nel nostro caso).
Vedremo in altra occasione come comportarci se si pretende una precisione
maggiore.
Il foro ottenuto non sarà esattamente coassiale
con la superficie cilindrica esterna, sempre
a causa dell'imprecisione dell'autocentrante. Se la coassialità delle due
zone è fattore essenziale
(e per giudicare di ciò, bisogna guardare alla destinazione del pezzo), le
due superfici, esterna
ed interna, devono essere finite senza muovere
il pezzo dall'inizio alla fine, cioè senza smontarlo dall'auto centrante
nelle fasi intermedie.
Ecco come si potrebbe procedere, partendo da una barretta della lunghezza di
circa 40 mm:
1) tornitura cilindrica esterna a 0 15;
2) intestatura;
3) esecuzione del foro di centratura;
4) foratura fino a g 6 per profondità fino a 22 -7- 23 mm;
5) torni tura interna fino a g 9;
6) separazione con seghetto della parte lavorata;
7) seconda intestatura fino alla lunghezza voluta della parte lavorata,
montata capovolta sull'autocentrante.
Tornitura fra le punte
Vogliamo ora costruire un alberino con Ø 12 mm e lunghezza di 100 mm.
In questo caso, data la rilevante lunghezza, la tornitura va eseguita fra le
punte.
Procuriamoci una barretta Ø 13 mm di acciaio (per passare a un materiale più
impegnativo e... meno costoso) della lunghezza di circa 112 mm, curando che
le estremità siano abbastanza lisce e perpendicolari all'asse.
Innanzitutto dobbiamo ricavare i fori di centratura alle estremità: per
questo, blocchiamone una
nell'autocentrante e spingiamo l'altra contro la punta da centro, come
abbiamo visto nel paragrafo
precedente, dopo aver controllato che giri abbastanza centrata.
Data la lunghezza del tratto a sbalzo, qui bisognerà sorreggerla con la mano
sinistra, mentre con la destra
si aziona la leva F; lavorare, quindi, a bassa velocità. Girato il pezzo, in
modo analogo si ottiene il foro
di centratura dall'altra parte. Questa operazione richiede indubbiamente una
certa abilità e molta attenzione:
ma, con la debita prudenza, non si faticherà troppo ad impratichirsi.
Sostituiamo ora all'autocentrante il platorello menabrida e collochiamo le
due punte (fig. 2 a), una nel foro dell'albero del mandrino e l'altra nel
cannotto della contropunta.
Infiliamo sopra un'estremità del pezzo la brida (figura 2 e) con l'appendice
verso l'esterno e stringiamo a fondo
la vite; poi imbocchiamo sulla punta della testa il foro di centra tura del
pezzo, in modo che la coda della brida entri in una delle tre asole del
platorello.
Spostando il supporto della contropunta, impegnamo la seconda punta nel foro
di centratura dell'altra estremità e blocchiamo il supporto sulle guide K
con la vite S. Con U regoliamo esattamente la posizione della contropunta
fino ad eliminare il gioco, ma in modo che il pezzo non sia troppo serrato.
Infatti, mentre la punta della testa gira assieme al pezzo, quella della
contropunta rimane ferma: bisogna perciò mettere un po' di grasso nel foro
di centratura per evitare surriscaldamenti durante il lavoro.
Regolata la contropunta, blocchiamo anche la vite V e assicuriamoci che
siano strette pure le viti E della testa.
Usando ora lo sfacciatore sinistro, riduciamo il diametro della parte vicina
81la contropunta a circa lO mm
su una lunghezza equivalente. Smontiamo il pezzo e, fissata la brida
sull'estremità lavorata, rimontiamolo
con gli stessi criteri in posizione capovolta.
Potremo ora, con lo sgrossatore sinistro eseguire comodamente le passate
necessarie dall'una
all'altra estremità fino al diametro voluto.
Attenzione! Prima di cominciare, accertarsi che la brida non vada a battere,
all'estremità della corsa,
contro il carrello o il portautensili. E controllare anche, dopo le prime
passate, .che la torni tura non risulti conica.
Per questo, misurare un'estremità del pezzo col calibro. presentandolo poi,
nella stessa posizione, all'altra estremità: se il calibro passa senza
forzare e senza gioco, la tornitura è perfettamente cilindrica.
In caso contrario... ahimé! è necessario provvedere alla correzione (a meno
ché il difetto non sia ritenuto irrilevante ai fini del risultato).
Se il diametro è maggiore dalla parte della testa, significa che qui la
punta è spostata verso l'indietro; e viceversa se questo diametro è minore.
Le due punte non essendo perfettamente allineate. avviene che l'asse del
pezzo non è esattamente parallelo alle guide: bisogna, dunque, girare la
testa
di quanto occorre per il perfetto allineamento delle punte.
Di ciò tratteremo, in modo indiretto, nel paragrafo che segue.
|